Back to the S1... I have been slowly getting it together to take it for an MOT, but the cold weather has not given me much interest in going into the garage.
I had the engine running a few weeks ago, and when I tried it again last week to take it for an MOT it wouldn't start. Grrrr. No spark.
Anyway, I have been trawling through the wires, and I think my biggest problem has been oxidation on the relay and fuse terminals. Some cleaning, then silicon grease and lots of push in, wiggle, take out etc. has got me some good contacts with considerable less voltage drop at the feed to the ignition unit.
Whilst doing this, I thought I would have a play with my oscilloscope from that well known manufacturer Rigol
It connects to my PC as well as having a USB slot. To be honest I have little knowledge of how to use it, but it does loads of stuff and the guys in the lab at work were well impressed with it. In reality I think it is a copy of a Tektronix.
Anyway, connected it up to the CPS and coil to look at the ignition events:
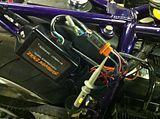
I captured a scope trace (I am still trying to get my head round how to do this well).
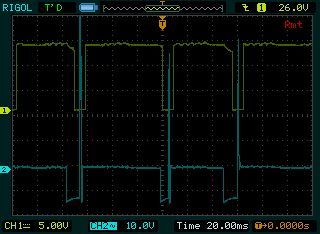
The yellow is the CPS, the drop corresponds to the gap in the rotor passing through the sensor. The blue is the voltage at the coil, and as all of you know, the spark is caused by the collapse of the magnetic field on the primary side, generating a rise in magnetic field on the secondary and a rise in voltage until the spark jumps from one electrode to the other. In fact, those eagled eyed people will see that the scope is connected the wrong way around on the coil as the dwell time (12V charge time) finishes at the point the spark is initiated (the spike - which is the collapse of the magnetic field on the secondary inducing a voltage on the primary).
You can get some info off the plot, such as engine speed and ignition timing...
So, the engine speed can be calculated from the time taken to complete a full revolution of the CPS rotor, it has two cut outs, so you need to count the time between the first and third rising edges. I reckon that is 130ms (20ms per square). One full revolution of the CPS is two crank revs, so it is 65ms per crank rev. 1/0.065 = 15.385 revs per second or 923.077 revs per minute.
You can also work out the ignition timing by calculating the number of degrees between the spark and the rising edge of the CPS. So I reckon that is 4ms (you really need a smaller timebase to do this accurately). Time per degree of rotation = 130 ms / 720 degrees = 180us, so 4ms is 22 deg crank angle, which is about right for
my ignition box with the VOES operational.
The funny thing is, none of this is new by any means. When I was a kid bombing around the estate on my 12" wheel bicycle, I used to see a van from time to time with wires coming out of the back connected to a car with an open bonnet with a guy opening the throttle with his hand. Once, I asked the guy what he was doing, and he said 'I am doing a Crypton Tune'. Wow, I thought. Best tell my dad... Anyway, IIRC, the guy with the van had a scope in the back and looked at the operation of points (remember them) and displaying the same as I am above.
I think Sun took the lead with this sort of kit, and Crypton (or TI Crypton) died a death.
But are there mechanics still using these great tools? I dunno, Rik will tell us, but I think the real answer is that cars are so sophisticated now that you just swap bits out rather than tinkering with electromechanical parts to get best performance <sigh>